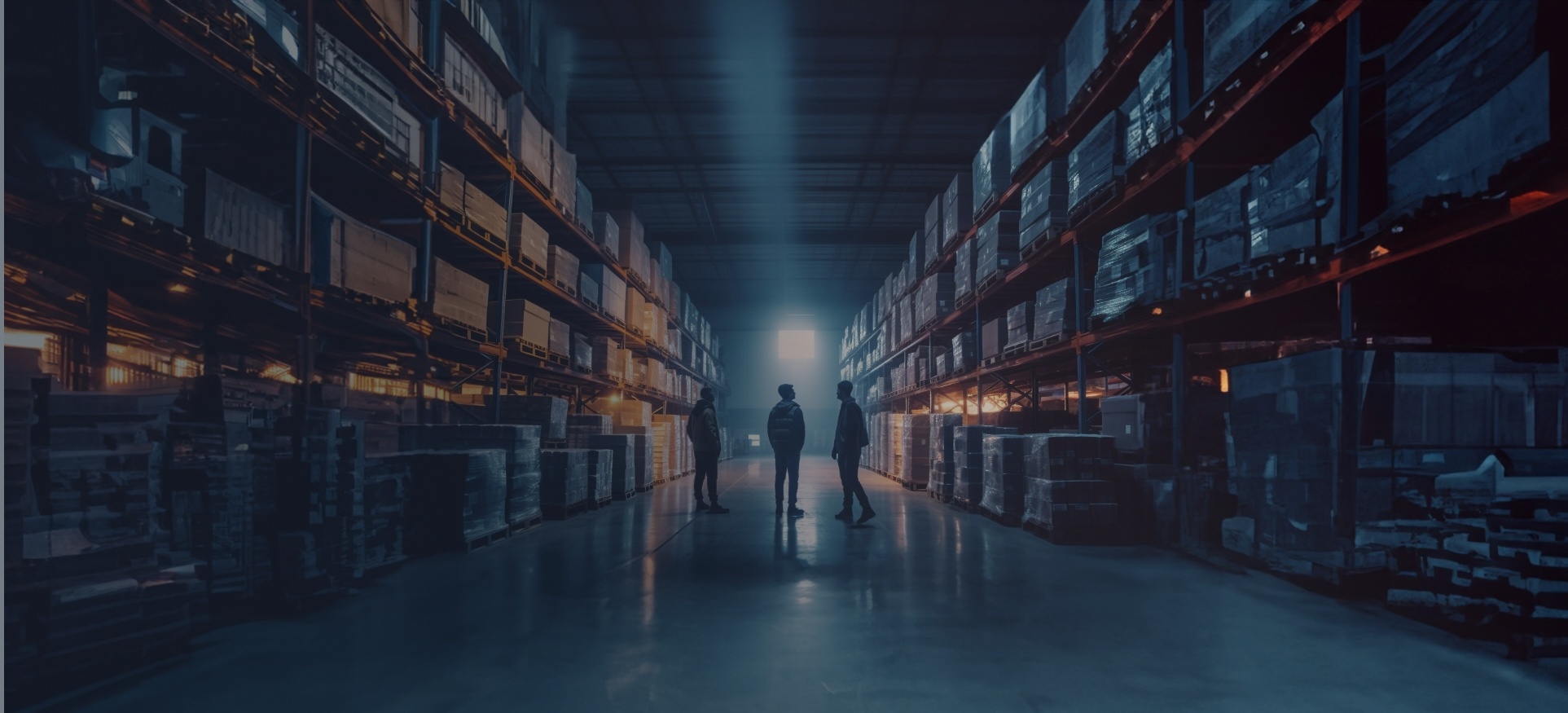
Shark WMS: Warehouse automation, swimmingly easy
Trusted by the best
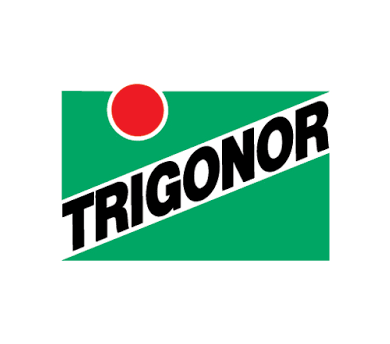
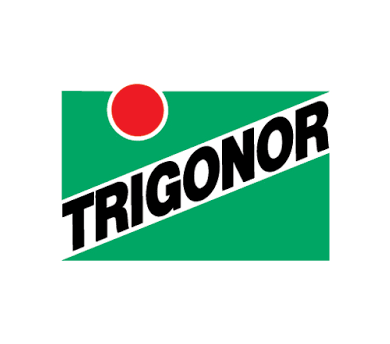
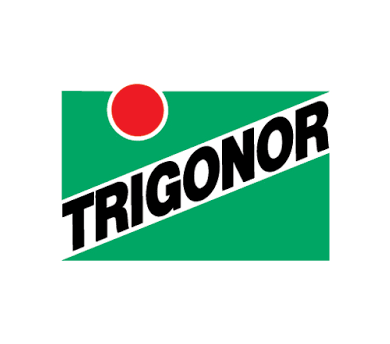
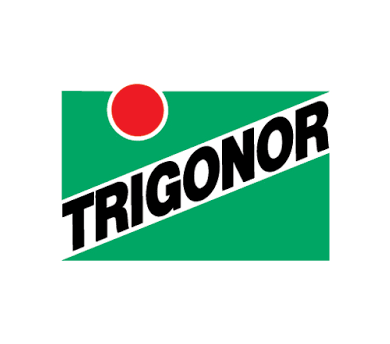
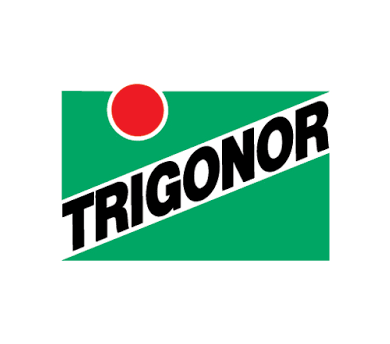
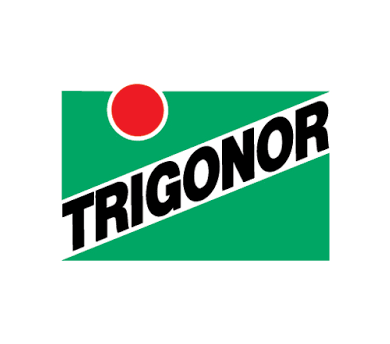
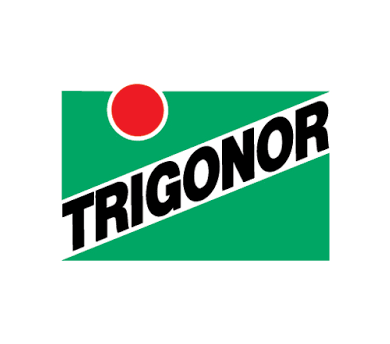
A warehouse management system that's easy to use
Warehouses are kind of like sharks: They should never stop moving.
A warehouse management system is the first step towards having your warehouse run by itself. Leave previously manual tasks to the most user friendly WMS on the market.
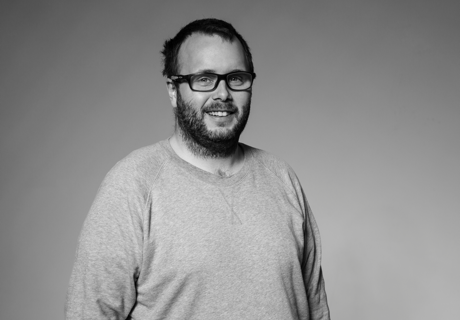
Unsure what you need? Hatch a plan with our advisors.
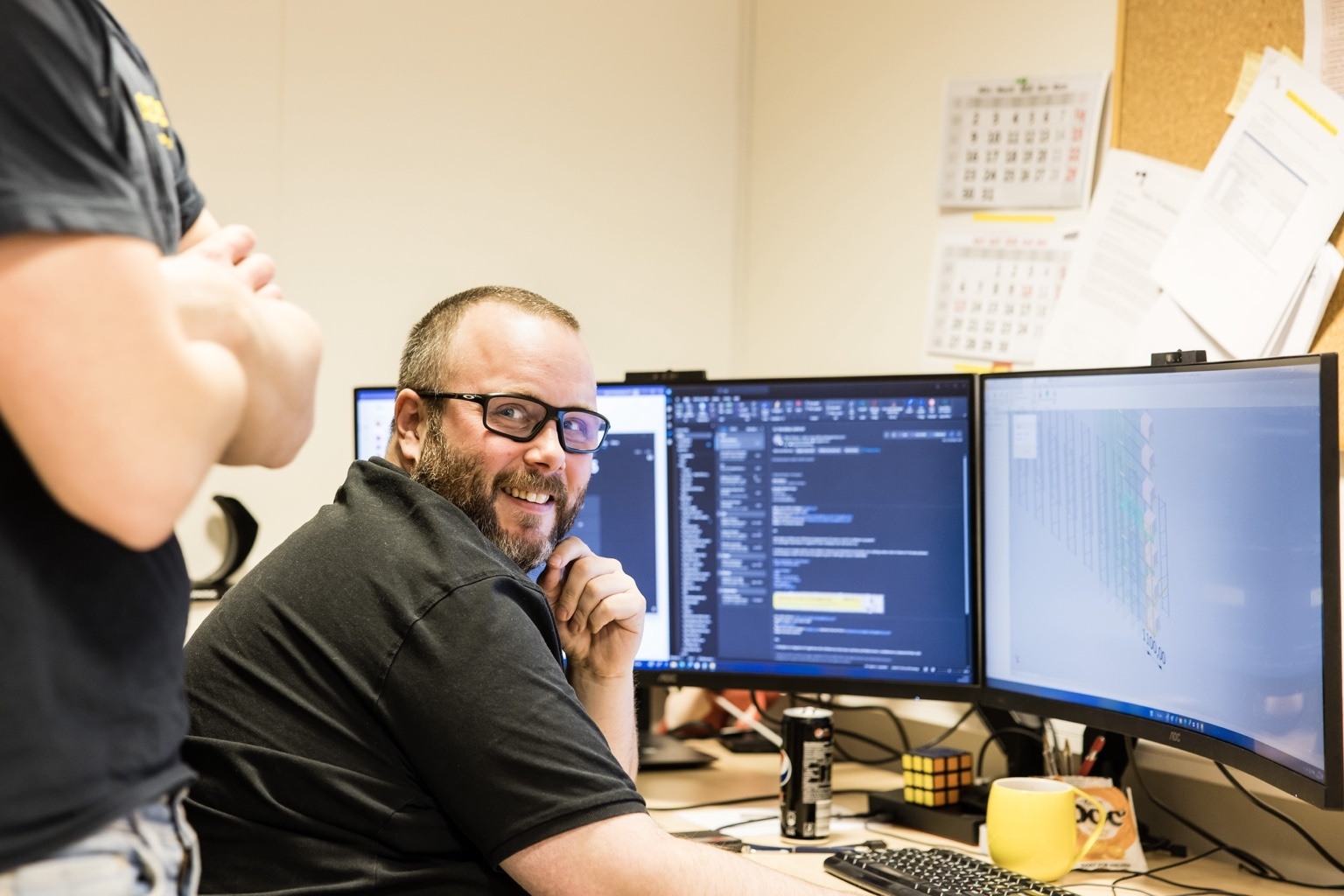
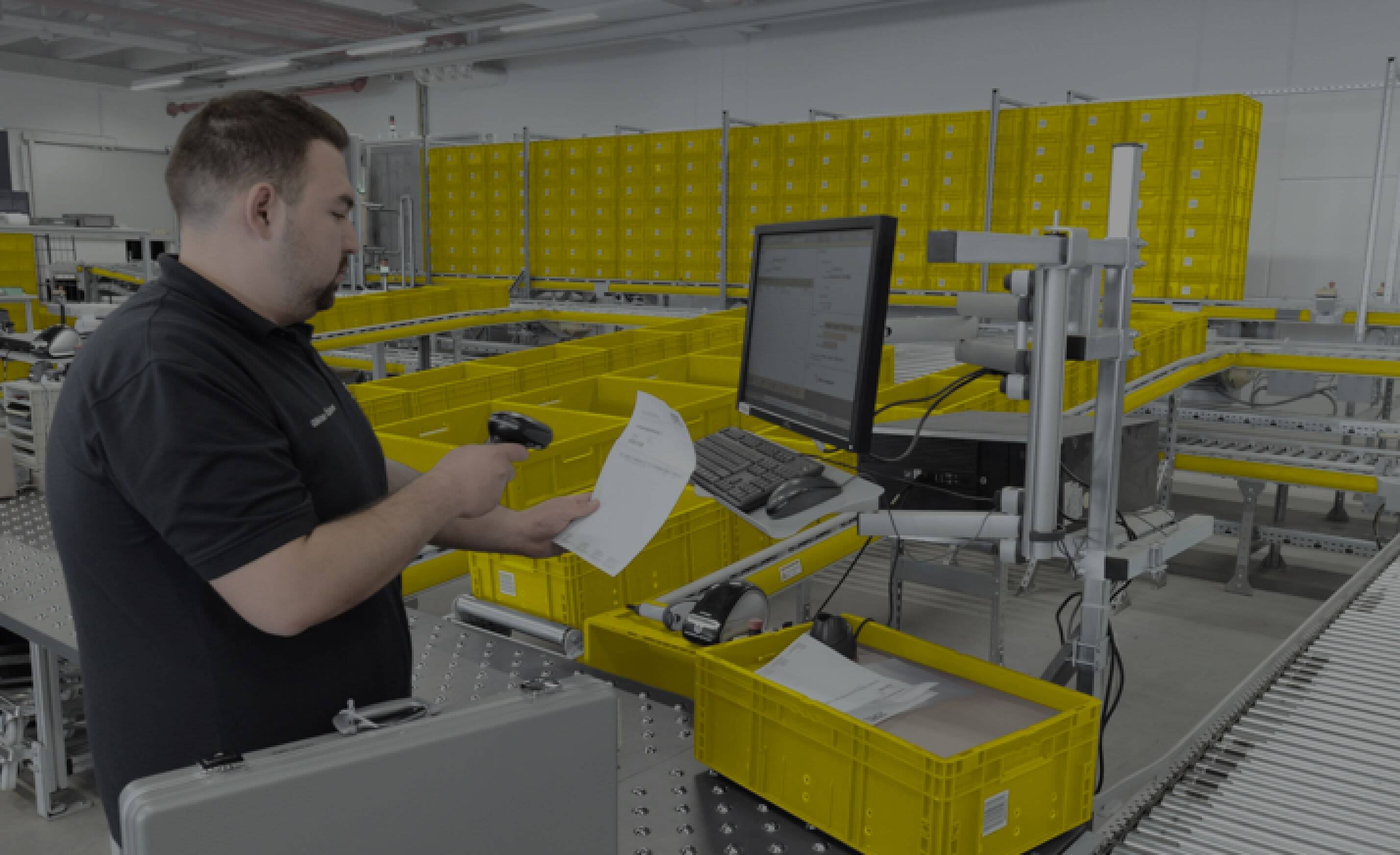
A WMS for warehouses of every size
Shark WMS is used by everyone from small ecommerce ventures to large scale firms. What they have in common is this: The WMS is always just as user friendly.
This by no means makes Shark a lightweight solution. Right beneath the hood, complex algorithms are running, hidden for the casual user. Shark actually makes it possible to get the best of both worlds.
8.813.976
Orders
113.720.307
Transactions
6.692.982
Locations
18
Languages
883.878
Lines of code
Podcast: “Master data is a hidden treasure"
Professor of Logistics Jakob Beer thinks digitalization is about to be a must-have for warehouses.
Podcast: The professor answers the listeners
Professor Jakob Beer is back to talk about how to handle new technology and higher cost of business for warehouses.
Think Shark WMS might be for you?
Have a chat with one of our advisors to see if Shark is a good fit.